Which Welding Process?
- Jasper Jasic
- Nov 7, 2018
- 3 min read
The welding process used is chosen based on the materials to be welded and the material thickness. Also to be taken into consideration is the production rate and visual aesthetics of the weld which may be on show.

Manual Arc (MMA)
This is one of the oldest processes and is still in common use. It is well suited to use welding outdoors and in repair work. It is a slow process however and requires a high skill level but can be used on a wide range of materials.
It can also be used in confined areas as the electrodes can be bent into shape for access. Equipment costs are lower than the other processes.
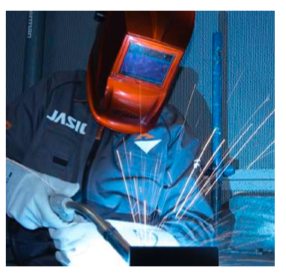
Metal inert/active gas (MIG/MAG)
The process is a common, versatile welding process. It provides high deposition rates and is suited to a wide range of material thicknesses, thin too thick. Compared with Manual Arc welding the process provides a weld with minimal weld finishing as there is minimal spatter and no electrode slag. It requires a low - medium skill level and has less problems to achieve good quality compared to TIG/MMA it has a narrow heat affected area. Its disadvantage is the torch is subject to a number of wear components such as contact tips, nozzles, liners etc. It is often a process that is automated to provide even higher production rates.
Flux Cored Welding (FCW)
Flux cored welding is a type of MIG/MAG welding using a standard MIG/MAG power source but uses a consumable which may contain a core of constituents which allow the process to self-shield itself therefore requiring no additional gas shield supply.
This makes it suitable for welding in areas where there may be draughts such as outdoors. In addition, consumables may contain elements to provide high deposition rates and hence productivity. The flux core however produces a slag coating which need to be cleaned after welding.

Tungsten Inert Gas (TIG)
TIG welding, is an arc welding process that uses a non-consumable tungsten electrode to produce the weld. The weld area and electrode is protected from oxidation or other atmospheric contamination by an inert shielding gas (argon or helium), and a filler metal is normally used, though some welds, known as autogenous welds, do not require it. A constant-current welding power supply produces the electrical energy, which is conducted across the arc through a column of highly ionised gas. TIG offers a high quality weld although generally a slower process compared to the others which requires a higher skill level.

Plasma Cutting
The basic principle is that the arc formed between the electrode and the work piece is constricted by a fine bore nozzle. This constriction increases the temperature and velocity of the plasma emanating from the nozzle.
The temperature of the plasma arc is in in excess of 20,000°C and the velocity can approach the speed of sound. When used for cutting, the plasma gas flow is high and creates a deeply penetrating high temperature plasma jet there by cutting through the material. The force of the arc blows away any molten material in the form of dross. The plasma process operates by using the high temperature arc to melt the metal.
The plasma process can therefore be used to cut metals including cutting metals which form refractory oxides such as stainless steel, aluminium, cast iron and non-ferrous alloys. The cut quality is dependent on many parameters but the system is easy to use and often is the only practical or cost effective solution.
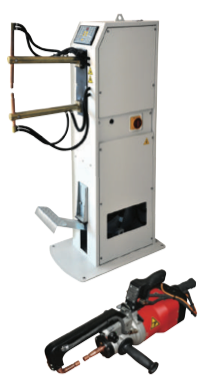
Resistance Welding (Spot)
Resistance welding (Spot) is also one of the oldest of the electric welding processes in use in the welding industry today. The weld is made by a combination of heat, pressure and time.
It is the resistance of the material to be welded to current flow that creates a localised heating in the material to be welded and hence the name resistance welding. The resistance of different materials will create different levels of heat for the same current passing through it. The pressure exerted by the electrode arms and electrode tips through which the current flows, holds the parts to be welded in intimate contact before, during, and after the welding current timecycle. The required amount of time current flows in the joint is determined by material thickness and type, the amount of current flowing and the cross-sectional area of the welding tip contact surfaces.
Process Comparison

Comments